日程計画法(スケジューリング理論)
- 山田 修司
- 2018年5月6日
- 読了時間: 3分
日程計画を決める際の計画方法には、「フローショップスケジューリング」と「ジョブショップスケジューリング」の2つがあります。
フローショップスケジューリングは、予定されているすべてのジョブについて、それぞれ実行されるべき作業が類似しており、かつ作業順序に従って設備が設置されている多段階生産方式(つまり、機械の配置に沿って、常に一方向に流れるような工場のライン。少品種大量生産や混合生産向き。)のスケジューリングに使用されます。
ジョブショップスケジューリングは、仕事の流れはあくまでも一本道、一筆書きの一方向であり、かつジョブについて実行されるべき工程順序や作業内容が異なるような多段階生産方式(例えば、オプションでカスタマイズ可能な車やスーツ。多品種生産向き。)のスケジューリングに使用されます。
また、作業を割り当てる順序についても検討が必要です。順序付けのための手法には、「順序付け手法」と「ディスパッチング手法」の2つのパターンがあります。
「順序付け手法」は、当該日程に付加されることが決定した仕事の各作業の加工開始・完了時点を「すべてあらかじめ」決定してしまう方法です。例えば、前もって前週までに来週の作業予定がはっきりわかっているようであれば、すべての順序をあらかじめ決定することができます。
「ディスパッチング手法」は、工程で一つの作業が完了するたびに、次にやるべき作業をその都度決めていく手法です。また、どの作業を選択するかという優先規則のことを「ディスパッチングルール」と言います。
ディスパッチングルールには、いくつかの選択肢があります。
先着順(FIFO):工程に先着で到着した順番に処理する
最小加工時間順(SPT):加工時間が短い順番に処理する
最小納期順(EDD):納期が近い順番に処理する
最大時間順:作業完了までの時間が最もかかる順番に処理する
最小スラック順(SLACK):スラック時間が小さなものから処理する。(納期 - 現時刻) - 残り総作業時間
納期を優先する場合には、最小納期順あるいは最小スラック順によるスケジューリングが裁量です。
尤も、現実の工程においては、あらかじめ順序付けされたジョブタスクが計画されていたにも関わらず、緊急案件の横やりが入ることで当初に計画した予定が乱されてしまい、あらかじめ順序付けによって決定された生産量を納期までに満たせなくなるようなこともあります。
そのような状況が多く発生するようであれば、月次の生産計画よりも週次の生産計画、週次でもダメなら日次の生産計画の管理に注力し、かつリードタイムの短縮化を図ることで現実の目標生産量に近づけやすくすることができます。(緊急案件を極力無くすか、いっそディスパッチング手法に切り替えてしまったほうが良い場合もあります。)
最近では、このようなスケジューリングをコンピュータで計画・管理しているような現場もありますが、コンピュータで計画する場合にも、計画に横やりが入った工程以降の後工程まで計画の入れ替えが発生することによって、あらかじめ納期に余裕を持って決めたはずの計画が、すべて崩れてしまうことがあるので注意が必要です。
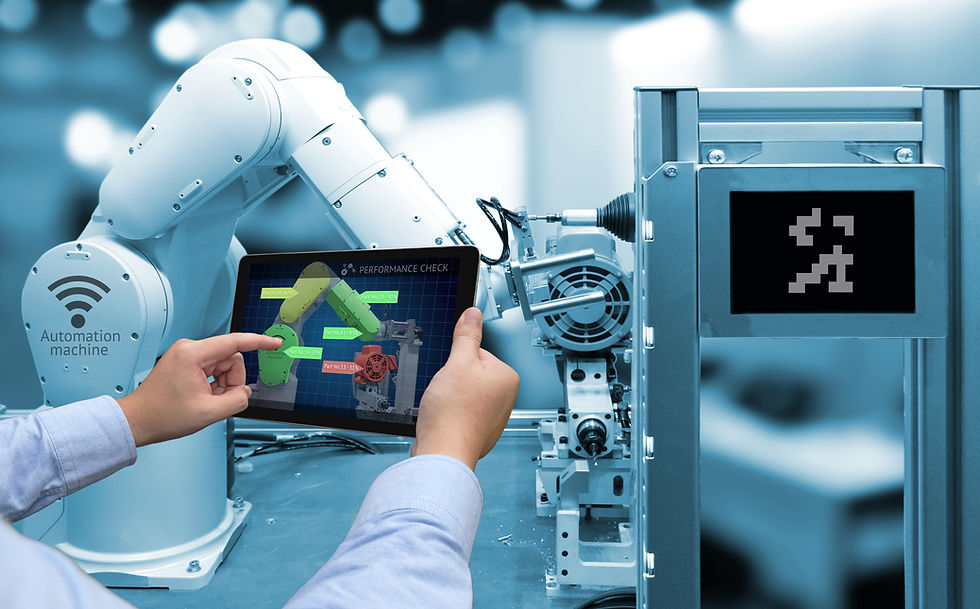
Comments